Избор между силиконово формоване и леене под налягане: Съвпадение на процесите с нуждите на проекта
В сферата на производството изборът на процеси на формоване е критично решение, което влияе върху резултата, разходите и ефективността на даден проект.Два широко използвани метода, силиконово формоване и леене под налягане, всеки носи свой набор от предимства на масата.Нека се задълбочим в предимствата на всеки процес, за да разберем по-добре кога и защо те блестят:
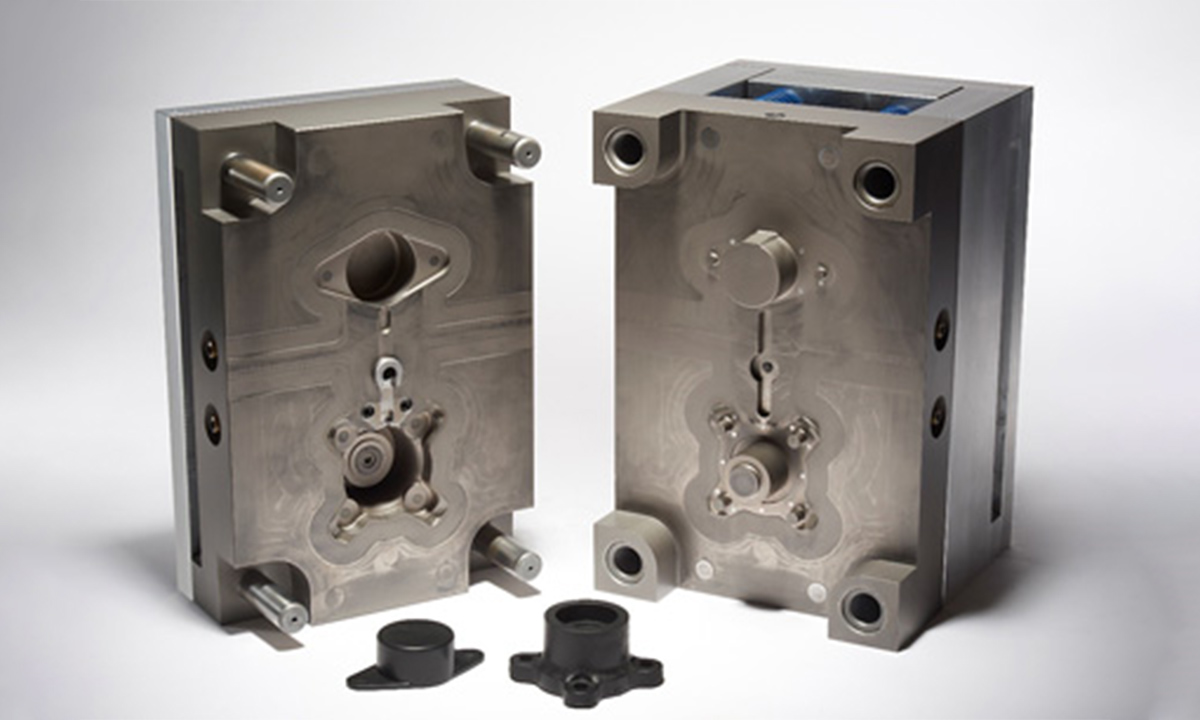
Инжекционно формоване
Силиконово формоване: Прецизност на изработката с гъвкавост
1. Гъвкавост: Силиконовите форми се отличават с гъвкавост, която им позволява да улавят сложни детайли с прецизност.Това ги прави идеални за изработка на сложни и деликатни части, обслужващи индустрии, където тънкостите на дизайна са от първостепенно значение.
2. Евтини инструменти: Инструментите за силиконови форми са значително по-евтини от инструментите за леене под налягане.Това предимство на разходите позиционира силиконовото формоване като рентабилно решение, особено полезно за малки производствени серии или фази на прототипиране.
3. Кратки срокове за доставка: Силиконовите форми могат да бъдат произведени бързо, предлагайки бърз обрат за проекти с чувствителни към времето изисквания.Това ги прави оптимален избор за начинания, които изискват скорост без компромис с качеството.
4. Съвместимост на материалите: Силиконовите форми показват съвместимост с разнообразна гама от материали, от смоли и пени до нискотемпературни метали.Тази гъвкавост в опциите за материали подобрява тяхната пригодност за различни производствени нужди.
5. Ниско налягане: Процесът на формоване на силикона включва по-ниско налягане, което го прави особено подходящ за материали, чувствителни към високи налягания и температури.Този нежен подход гарантира целостта на деликатните материали.
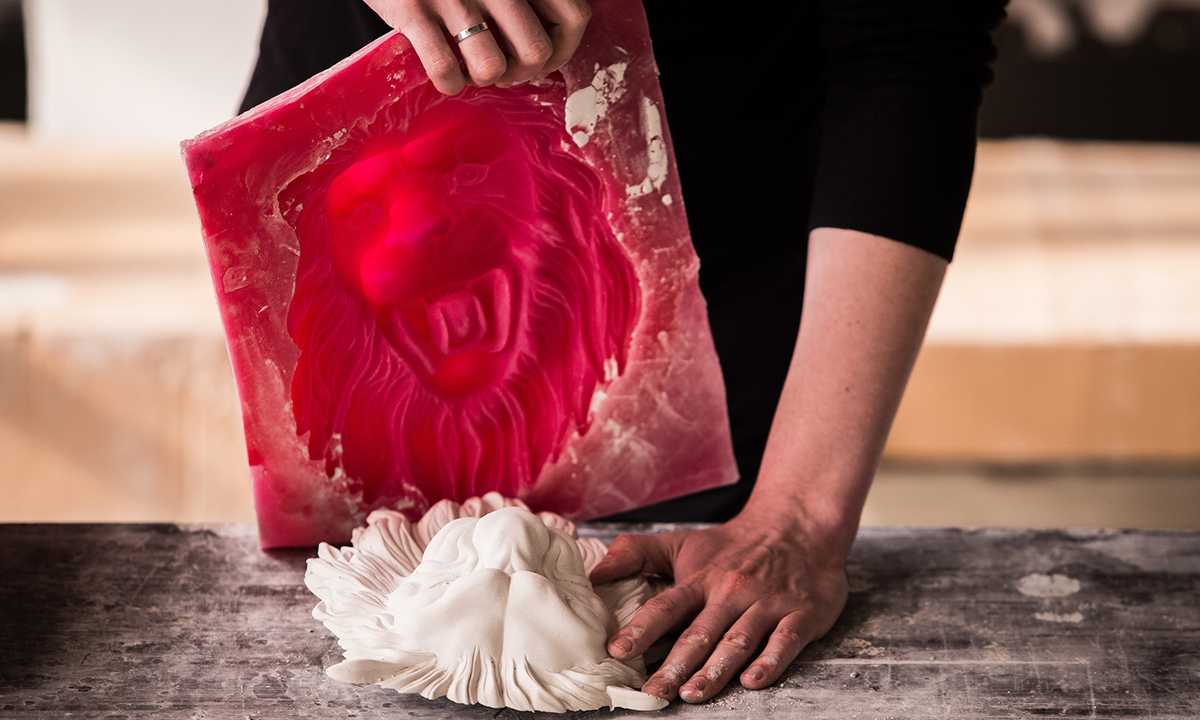
Силиконова формовка
Шприцоване: Ефективността на прецизността на големия обем
1. Производство в голям обем: Инжекционното формоване е водещо, когато става дума за производство в голям обем.Неговата ефективност и скорост, след като първоначалната инструментална екипировка е поставена, позволяват автоматизирано производство на големи количества части, което го прави предпочитан избор за масово производство.
2. Последователност и прецизност: Процесът на леене под налягане гарантира висока повторяемост и прецизност, решаващи фактори за индустриите, където постоянното качество във всички произведени части не подлежи на обсъждане.Тази надеждност е особено ценена в сектори като автомобилостроенето и електрониката.
3. Широка гама от материали: Инжекционното формоване поддържа широк набор от материали, обхващащи инженерни пластмаси, еластомери и метали.Тази гъвкавост го прави приложим за широк спектър от индустрии и приложения.
4. Сложни форми и тесни допуски: Прецизността, постижима с леене под налягане, позволява създаването на сложни геометрии и тесни допуски.Това го прави предпочитаният метод за части, изискващи високо ниво на детайлност и точност.
5. Ефективност на разходите (за големи тиражи): Докато първоначалните разходи за инструментална екипировка може да са по-високи, разходите за част намаляват значително с по-големи производствени количества.Тази ефективност на разходите при мащабни операции поставя леенето под налягане като предпочитан избор за тези, които търсят икономии от мащаба.
Избирайте мъдро: Съгласуване на процеса с проекта
В заключение, решението между силиконово формоване и леене под налягане зависи от няколко фактора, включително желаното количество части, сложност на дизайна, изисквания за материали, прецизни спецификации и бюджетни ограничения.За по-малки тиражи, прототипи или сложни части, гъвкавостта и рентабилността на силиконовото формоване може да преобладават.Въпреки това, когато се цели производство в голям обем, постоянно качество и ефективност на разходите, леенето под налягане често се очертава като оптималното решение.Ключът е в разбирането на уникалните силни страни на всеки процес и привеждането им в съответствие със специфичните нужди на конкретния проект.
Време на публикуване: 19 януари 2024 г